Te presentamos un artículo de B&R donde aborda el sistema de transporte de piezas de trabajo. Esperamos que te sea útil pero sobre todo queremos que conozcas los avances de automatización que esta excelente marca ofrece.
El sistema de transporte ACOPOStrak de B&R se utiliza en un sistema de inspección por rayos X para celdas de batería redondas. Con máxima flexibilidad, operación en paralelo simple en varias líneas y un flujo de producción altamente controlable, este sistema combina un funcionamiento rentable con un rendimiento de prueba impresionante.
Aunque la producción de baterías representa solo una pequeña parte de la producción total de vehículos eléctricos, su importancia económica y estratégica es inmensa. La aceptación y la penetración en el mercado de vehículos dependen de la calidad y el precio de los sistemas de almacenamiento de energía móviles.
Aproximadamente un tercio del coste de un vehículo eléctrico se debe a la batería. La autonomía del vehículo, que depende de la capacidad de la batería, sigue siendo la característica más importante para la mayoría de los compradores. La calidad y la fiabilidad de las baterías tienen un impacto directo en la seguridad y las características de conducción. Por ello, es esencial una inspección del 100 % de las baterías durante la producción. La inspección por rayos X se ha establecido como un método común para la inspección en línea de baterías.
Inspección por rayos X a 175 células redondas por minuto
Exacom GmbH de Hannover está especializada en la inspección de celdas de batería prismáticas y redondas.
La empresa suministró el sistema iXcell para la inspección por rayos X de celdas redondas a la gigafábrica de un conocido fabricante de vehículos eléctricos. Para alcanzar la velocidad de inspección requerida de aproximadamente 175 celdas por minuto, se utilizó en el sistema un sistema de transporte ACOPOStrak de B&R Industrial Automation.
Hagen Berger, director general de Exacom, explica: «Básicamente, hay dos factores decisivos para la inspección por rayos X: tenemos que dominar la adquisición de imágenes, lo que significa utilizar un proceso que capture una imagen de alta calidad con la máxima fiabilidad en el menor tiempo posible, y también necesitamos un sistema de transporte adecuado».
En toda la planta de producción de baterías de la gigafábrica del fabricante de coches eléctricos se utiliza ACOPOStrak de B&R. La inspección por rayos X con iXcell está totalmente integrada en la línea de producción y examina cada celda de la batería durante los pasos críticos de producción y la expulsa inmediatamente si falla la prueba. Esto significa que las celdas defectuosas no son arrastradas a través de todo el proceso para luego ser expulsadas al final de la línea, lo que provocaría pérdidas de rendimiento, materias primas y energía.
La integración en línea de las estaciones iXcell también significa que el sistema de rayos X debe seguir el ritmo del flujo de producción y no convertirse en un cuello de botella. Entre 150 y 175 celdas de batería por minuto salen de las máquinas de bobinado automático en la producción de celdas de batería y cada una debe probarse en una ventana de tiempo de aproximadamente 340 milisegundos. Hagen Berger: «Para cumplir con este requisito, utilizamos las posibilidades del sistema de transporte ACOPOStrak. Durante la inspección, la lanzadera individual con la celda de batería debe permanecer absolutamente quieta. Cada vibración posterior a la parada prolonga el ciclo de prueba. Por eso, los especialistas de B&R configuraron el controlador del sistema de transporte de manera que la celda en la estación de rayos X se ralentice con la mayor desaceleración posible y un perfil de movimiento predefinido y la vibración se suprima al máximo.
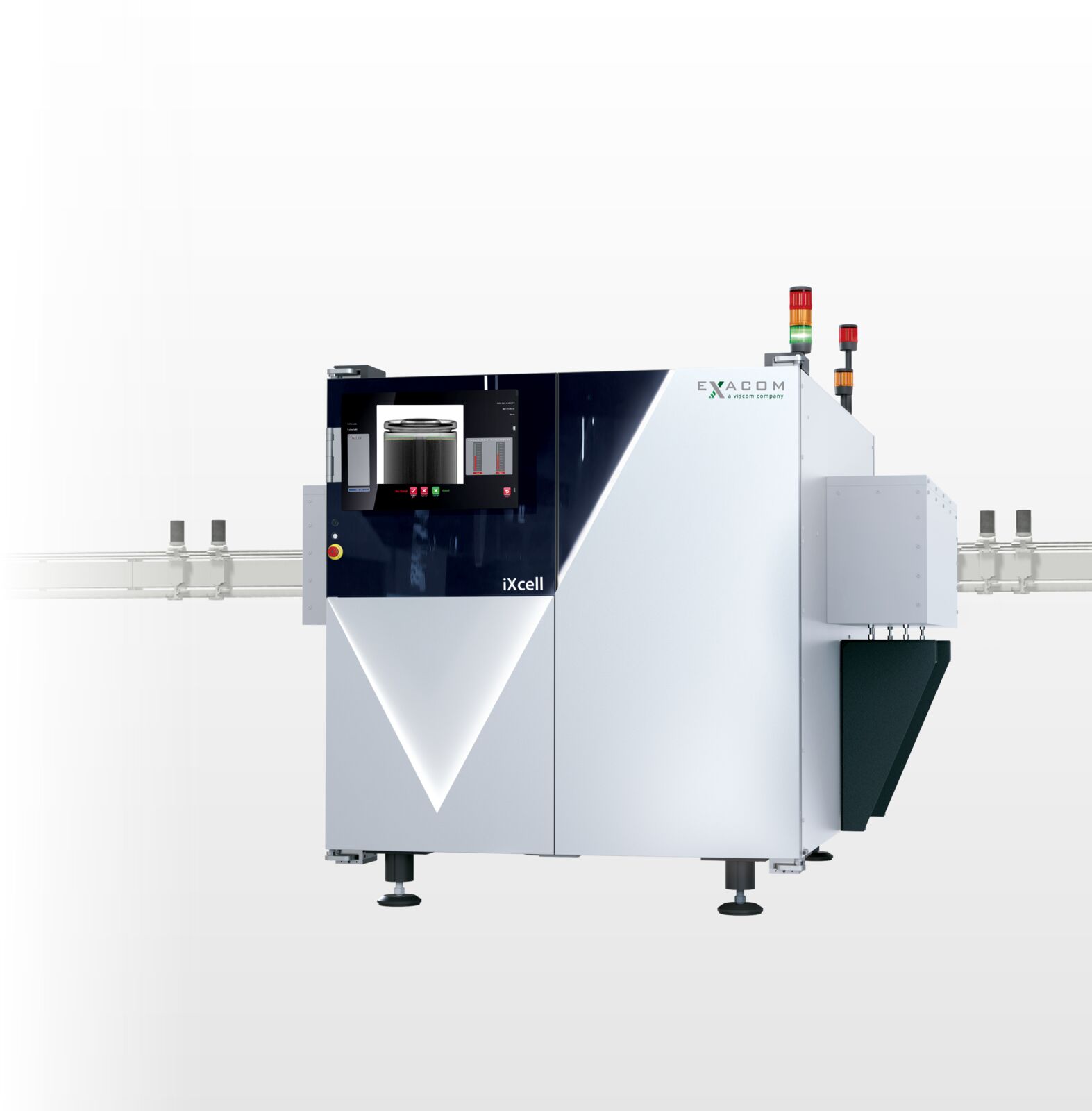
Máxima flexibilidad en el diseño del sistema como elemento innovador
Pero, sobre todo, el director general Berger considera que la flexibilidad casi ilimitada del diseño del sistema ACOPOStrak es un punto fuerte: «A diferencia de un sistema de monorraíl convencional, B&R ofrece un alto grado de flexibilidad en el diseño del sistema global, especialmente a la hora de conectar diferentes pasos del proceso. El desviador electrónico nos permite expulsar fácilmente las células defectuosas, establecer flujos de producto paralelos o, en caso necesario, dirigir el proceso a una estación específica sin tener que interrumpir la producción, por ejemplo, para realizar tareas de mantenimiento. Hasta donde yo sé, ningún otro fabricante puede hacer esto de esta forma».
Berger explica lo que esto significa en la práctica con un ejemplo: «El diseño del ACOPOStrak permite recoger las células redondas de cuatro bobinadoras en la giga-fábrica y pasarlas por dos sistemas de rayos X. Gracias a la flexibilidad de trayectoria, podemos incluso trasladarnos a una estación de giro si es necesario, lo que permite pasar una célula con una muestra de prueba girada 90 grados por un sistema una segunda vez».
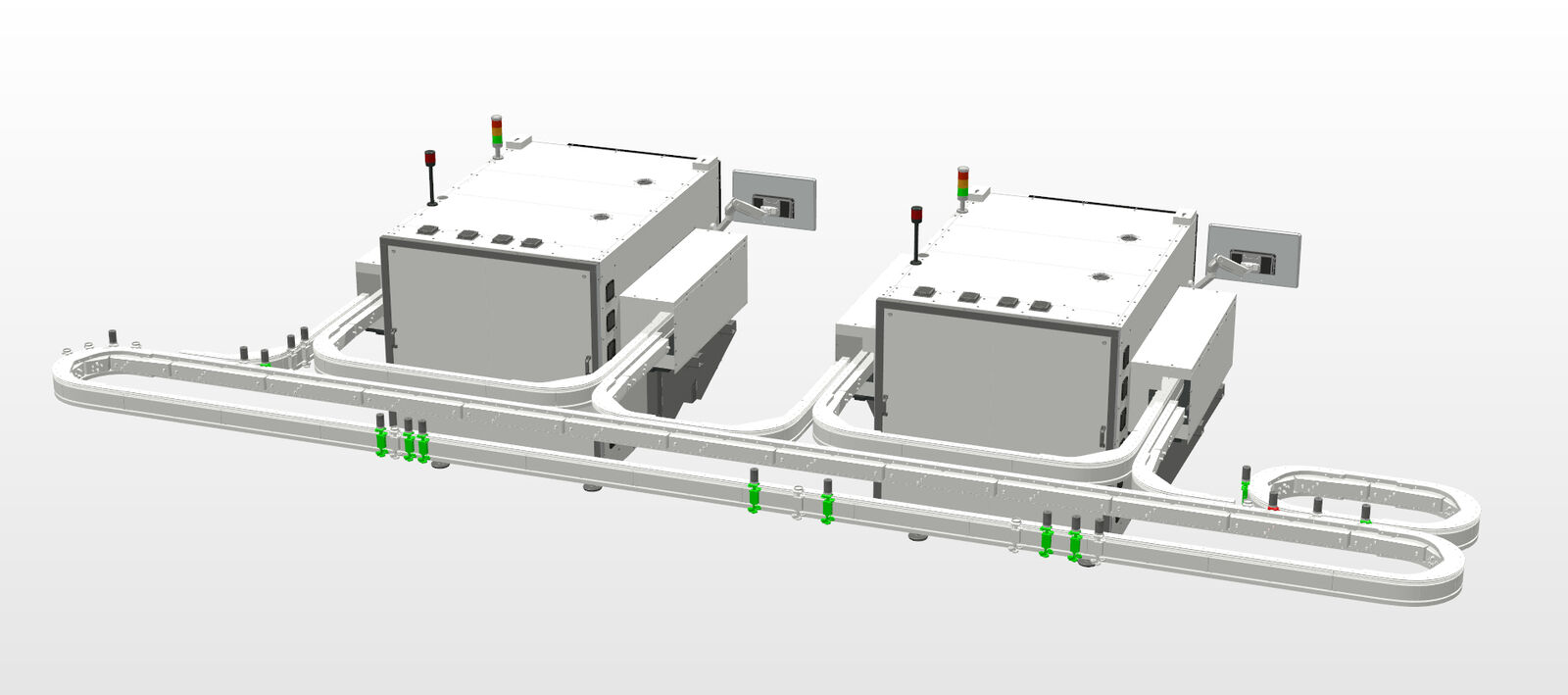
Alcanza tu objetivo más rápido con un gemelo digital
Para el diseño del sistema de rayos X, desarrollado especialmente para este fabricante de baterías, Exacom contó con el gemelo digital ACOPOStrak y con el apoyo de ingeniería de la sucursal de B&R en Hannover y de la sede central en Eggelsberg, Austria. «Tuvimos que diseñar el sistema de rayos X en un plazo de seis meses e integrarlo en la producción de baterías. Fue un desafío y realmente agradecemos el apoyo de B&R», explica Berger.
En un tiempo muy breve, se probaron y definieron el diseño del sistema y las posiciones en las que las muestras de prueba entran y salen del sistema de rayos X con la ayuda de una simulación digital. Esto también implicó encontrar un diseño de línea adecuado para optimizar la manipulación de las muestras de prueba de baterías, incluyendo el almacenamiento intermedio, la descarga y el flujo de material. Berger resume con satisfacción: «Este desarrollo acelerado dio como resultado menos pruebas y errores y nos permitió determinar en una etapa temprana del proceso de desarrollo cómo debían colocarse las celdas y los soportes».
Para Exacom, un efecto secundario positivo de la simulación con un gemelo digital fue la posibilidad de transferir el código fuente de los modelos de simulación directamente al hardware. «En general, un gran trabajo en equipo», concluye el director general Berger.
Esperamos que el artículo haya sido de tu interés y te recordamos que en DOMUN AUTOMATION estamos a tus apreciables órdenes. Contáctanos para cualquier duda o aclaración. ¡Somos tus aliados en automatización!